Member Spotlight: Donnie Deyoung
Donnie Deyoung
The Air Barrier Association of America (ABAA) dives inside the career of Donnie Deyoung
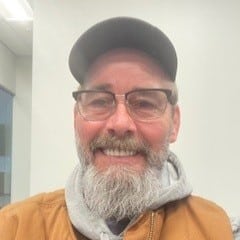
Name: Donnie DeYoung
Title: Waterproofing and Firestop Superintendent
Firm: Alpha Insulation and Waterproofing
City: Round Rock Texas
I’ve been in this industry for 20 plus years and still love what I do every day. I was an estimator for a glazing industry prior to getting into waterproofing. I’m a proud grandparent of 8 grandkids and have been with my wife for 16 years.
In my off time, I enjoy hunting, skeet shooting, playing golf, working on older model cars and spending time with my friends and family. I also have 3 dogs (blue heeler Zoey, Staffshire Pit Terrier Oliver and a Shepard, Lab mix Dixie that keep me busy.
DO NOT USE - USED TO KEEP ACCORDION CLOSED INITIALLY
What's a project you've worked on that you're especially proud of and why?
A: 600 Guadalupe is the one that comes to mind. It was at the time the tallest building in downtown Austin at 68 stories. I started that job in March of 2018 three stories below grade and completed our scopes on level 68 around April of 2024. It was the most challenging projects in my 20 plus years in construction.
How does proper air barrier installation contribute to overall building performance and sustainability?
A: With a proper install, you save on building costs with HVAC, maint,.costly repairs and overall life of the building. Helps with keeping the building from getting mold, or other unsightly conditions due to air and moisture leaks that go unforeseen until it’s too late.
How has earning your Level 3 Certification impacted your career and business opportunities?
A: Getting my level 3 has opened up new challenges, created a broader scope of work, and has allowed us to go after work that without ABAA certified classifications, would not be possible. It also expanded our clientele base and built new relationships.
What's one challenge you've faced in the field, and how did you overcome it?
A: One thing that comes to mind is the proper way to detail openings and ensuring everyone does it consistently and per details. Constant and consistent training with installers coming on board. It helps reduce and eliminate bad habits and wrong installations.
How do you educate clients or general contractors on the importance of air barriers?
A: I’ve always found it more effective to talk face to face and present our clients with the product data, installation guides and any additional tech talks or literature we can find to help them get the best understanding. It’s also beneficial to have the product reps come by and do a short presentation of the materials being used on their projects.
What's a common mistake you see in air barrier installation and how can it be avoided?
A: I tend to see a lot of reversed laps and wrong thru wall flashings being used for specific conditions and or materials that aren’t compatible. Precon meetings with your clients and their third-party inspectors can be very productive to review drawing details, transitions and sequencing to help eliminate those types of mistakes.
What tools or technologies have made the biggest impact on how you do your job?
A: Going wireless with equipment like tablets, smartphones and having the proper up to date info required to complete a project is huge in my opinion. So many new apps and software out there to help you manage your projects more effectively and communicate as well.
What do you wish more people understood about the work of air barrier installers?
A: The actual dangers we as installers face every day with the products we install, or the access we have to create at times to get to places that require extreme heights, or being in confined spaces with harmful chemicals and being in trenches etc. Our people risk their lives every day in our line of work. Sometimes we get asked to do things that push our limits because people don’t take the time to plan or sequence scopes.
How do you stay up to date with industry standards, training, or new installation techniques?
A: Utilizing the internet to keep up with current as well as new products that seem to be popping up more and more. Training in classroom as well as field with the product reps and keeping up with current installation techniques, changes etc.
If you could change one thing about the industry, what would it be and why?
A: I’d have to say the one change would be to find a way to make products more compatible with each other to make installations easier for our field teams and more cost effective for our budgets. ( I know that’s two answers but I felt they were equally important.)