Member Spotlight: Stephen Owens
Stephen (Steve) Owens, 34, husband and father of 2, US Army veteran. Since I was young, I have always enjoyed the outdoors and outdoor activities. Naturally, that led to my gravitation towards the construction industry around 2012. My primary specialties include masonry, air barrier, and waterproofing systems in and around mainly VA, DC, MD, and NY. I began my journey in the world of air barriers from the start, as it was a specialty for my employer at the time. Some notable projects I have participated in include projects across Cornell University in Ithaca, NY, Museum of the Bible and several parcels at the Wharf in Washington D.C.
What’s a project you’ve worked on that you’re especially proud of, and why?
A: Over the last couple of years, I have worked on several projects at Cornell University, and the new College of Computing and Information Science building stands out. I was tasked with installation and quality control of the waterproofing and air barrier systems. It has been a fairly challenging project, but we were able to accomplish a great deal with the help of a great crew of craftworkers, support from the general contractor, and cooperation from fellow subcontractors.
How does proper air barrier installation contribute to overall building performance and sustainability?
A: In my opinion and from my experience, one of the largest contributions is moisture management. Failure to install correctly, gaps in continuity, incompatible materials at tie-in locations with other systems, physical damage, and even UV overexposure can all lead to failures in the system. In the aspect of moisture control, failures lead to further damage of the system, degradation and shorter life span of substrate materials, higher energy costs from further air leakage, and higher costs for repairs.
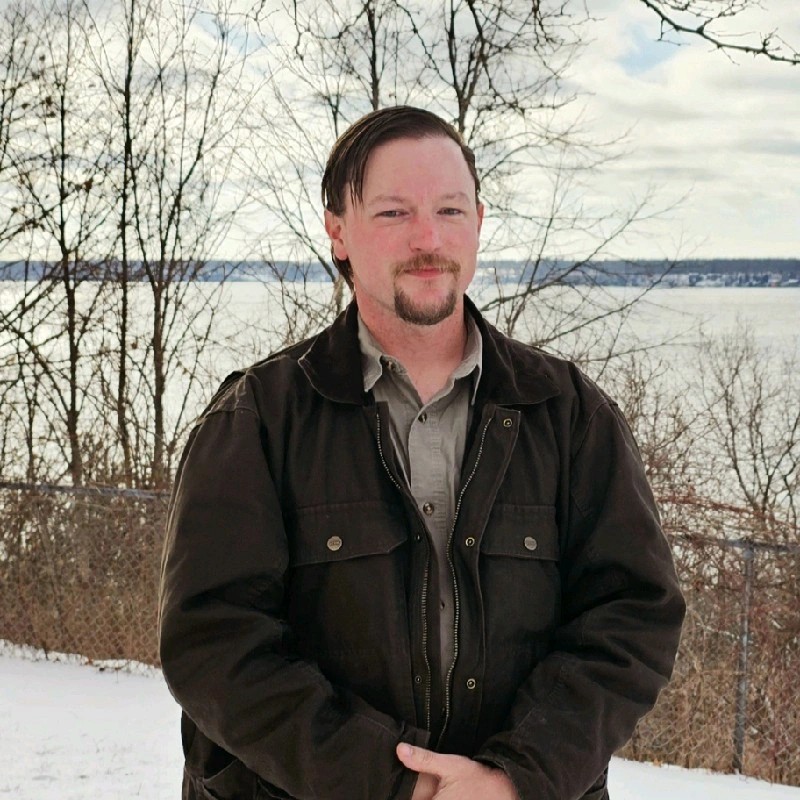
Name: Stephen Owens
Title: Foreman, BAC Local 2 PCC/Mason Journeyman
Company: Lupini Construction Inc.
City: Evan Mills, NY
How has earning your Level 3 Certification impacted your career and business opportunities?
A. To say advancement to a Level 3 Certification has had a positive impact would be an understatement. It validates time and experience in the world of air barrier systems, which is invaluable in many areas where the standards are increasing. I feel the largest impact has been the shift from being a follower to being more of a teacher. While still performing installations and always looking for new things to learn, I find myself teaching more and more people as I go, with extra attention to those just starting out.
What’s one challenge you’ve faced in the field, and how did you overcome it?
A. I had a task that required repairs to a damaged fluid applied system. We had very little room for error, with a tight timeline and the conditions working against us. I completed the repairs and made sure to give myself an extra day as a buffer, which thankfully helped to identify the repair materials failing from a bad batch. It all worked out in the end and passed inspection due to proper planning and giving myself that extra day. If something can go wrong, it will, likely at the worst of times.
How do you educate clients or general contractors on the importance of air barriers?
A. As a visual learner myself, I always try to use physical examples and drawings when teaching others. I also keep photos from current and past projects available to reference for myself and to show others. Especially in cases where conditions are unusual and not typical, past examples can be a great tool to demonstrate proper detailing and possible solutions for what obstacle you may be facing. Examples of damage is a great way to demonstrate the importance of proper installation.
What’s a common mistake you see in air barrier installation, and how can it be avoided?
A. Incompatibility of materials at tie-in locations with other systems, which brings up the “by others” dilemma on shop drawings. More questions need to be asked before drawings are even approved. “Will the glazier’s sealant be compatible with the air barrier system and sealant?” “Will the roofing membrane be compatible at tie-in locations?” A few examples I have personally experienced, that have all received multiple stamps of approval before issues arose during the installation phase.
What tools or technologies have made the biggest impact on how you do your job?
A. Expedient application materials. From quick spray and dry primers in tanks, primerless self-adhered membranes, one-part cold applied liquid coatings, to even pails of one-part caulk and sealants. Time is valuable, even more so when making repairs, because damages on construction sites happen. On days when time is limited due to weather or other circumstances, they also make it possible to continue work on areas you may not have enough time to complete otherwise.
What do you wish more people understood about the work of air barrier installers?
A. Air barrier installation is like an iceberg. On the surface, so many people think it is just excess waterproofing, painting, and putting stickers on the wall. However, there is quite a bit more depth to it. We are expected to see and know the bigger picture. From substrate preparations and conditions required, compatibility with different systems and materials, to manufacture specified detailing and remediation. Disregard for proper installation can sink a project’s timeline and budget.
How do you stay up to date with industry standards, training, or new installation techniques?
A. I take advantage of the yearly training provided by my employer and the Bricklayers and Allied Craftworkers Union. I work with representatives from the different manufacturers, who also have a great deal of knowledge to share, demonstrations, and training events. Most reps I have worked with were more than happy to share techniques they have seen along the way. In my spare time, especially before the start of a new project, I brush up and read through applicable specs and tech data sheets.
If you could change one thing about the industry, what would it be and why?
A. Easier access to training and certifications. Even for me, there are still products I cannot get certified or trained on unless I am at the right place at the right time, or assigned to the right project. Everyone in the trade should have easier access in order to broaden their horizons and improve their professional value in the market. More opportunities can lead to more people learning and taking part in building enclosure systems.